Sustainability as a corporate objective
Climate protection, preservation of our environment, and conservation of natural resources are among the most pressing issues worldwide. As a company in the automotive industry, GRAMMER has a special responsibility to lead by example. In 2021, we therefore launched a comprehensive program with the aim of operating even more sustainably worldwide. The aim was to reduce CO2 emissions by at least 50 percent by the end of the decade. We can today say with pride that we have actually made faster progress than originally planned.
With our Green Company initiative, we are building on our most important resource: our employees across the globe, who are transforming GRAMMER into a Green Company with their good ideas and wide-ranging areas of expertise. Since this initiative was launched, we have been implementing more and more projects to save energy, avoid waste, recycle raw materials, and make production processes more environmentally friendly. One of our most important action areas in this regard is the development of sustainable products from environmentally friendly materials. In this way, we are also supporting the automotive industry in further refining and optimizing its products.
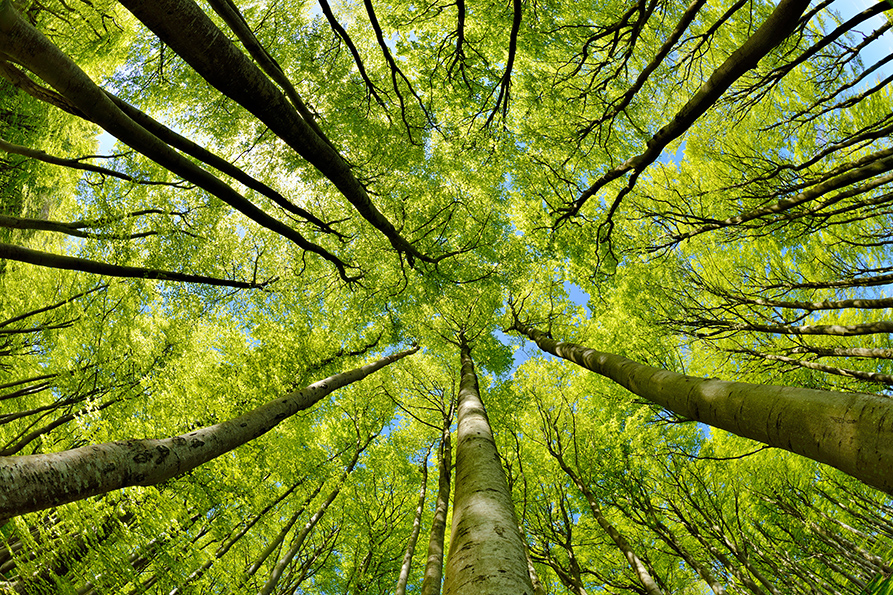
Holistic environmental protection
Holistic environmental protection is a very important part of our corporate philosophy. Our corporate principles define active protection of the environment as an important goal. We make our contribution by developing and producing our products using environmentally friendly production as well as through hazard-free use and disposal.
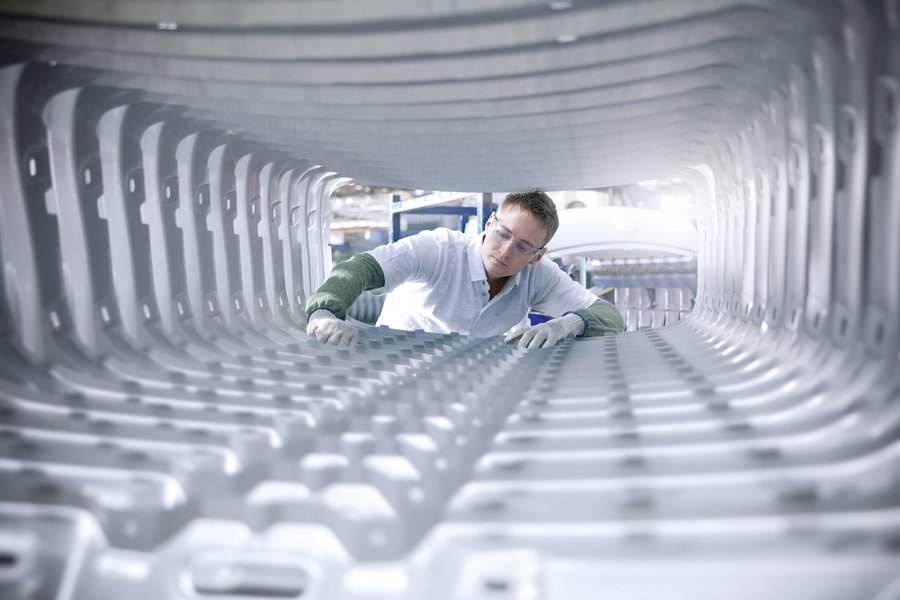
A passion for top quality
Our work needs to be flawless in order to meet the needs and expectations of our internal and external customers. Maintaining our high quality standards and continuous improvement are our ongoing tasks.
Social responsiblity
To us, sustainability means more than protecting the environment. It also involves assuming social responsibility by balancing the interests of our shareholders, employees, and customers and those of the social environment in which we operate.
GRAMMER AG has therefore launched numerous initiatives to support social and cultural projects and educational institutions in the Oberpfalz region as well as at many other locations worldwide.
GRAMMER is aware of its responsibility and is committed to the core labor standards of the International Labor Organization (ILO) and the United Nations Universal Declaration of Human Rights.
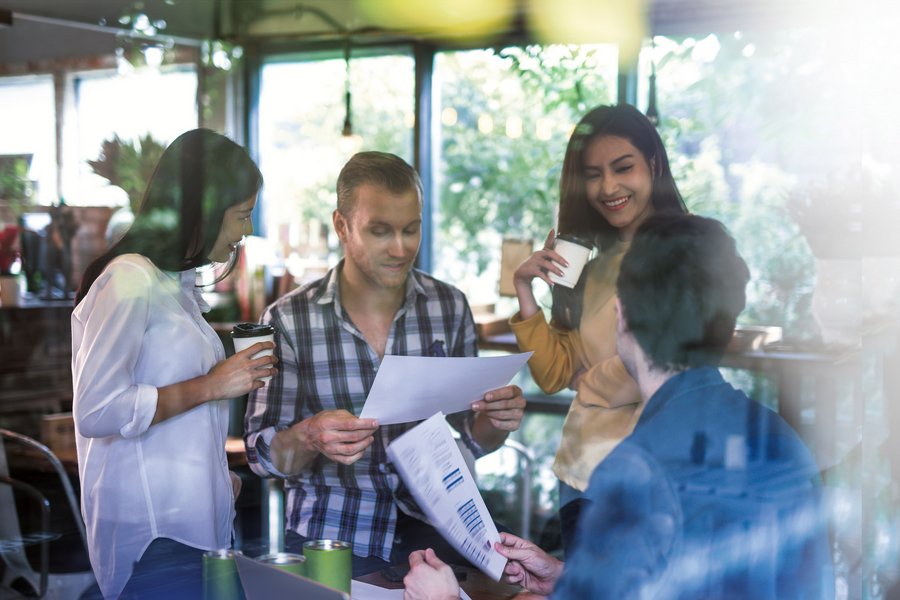
Our employees: the basis of our success
Our success is based on the high level of training, creativity, and commitment of GRAMMER employees around the world. We support the qualification and development of our employees and strengthen their personal responsibility in their professional tasks. We lead and act according to the principles of trust, responsibility, openness, honesty and equal opportunity.
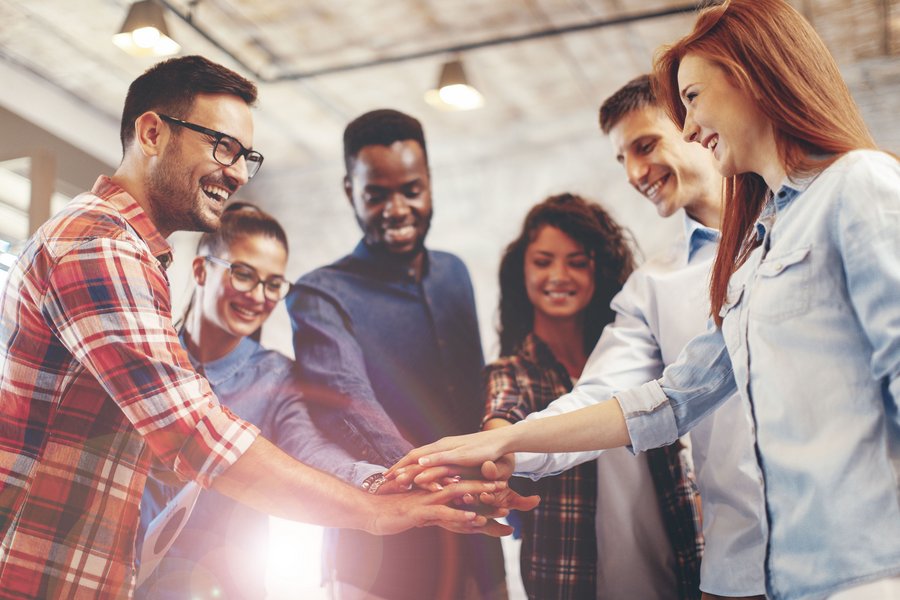
Human Rights
With our policy statement, we commit ourselves to strengthening respect for human rights in our own business and along our value chain and to preventing human rights violations. It is regularly reviewed, adapted and further developed.
Diversity
Our highest guideline: Equal opportunities, i. e. no privileges, no disadvantages in the workplace. Therefore full satisfaction and fair development opportunities for all Grammer employees worldwide.
In our corporate guidelines the principles of equal opportunity are firmly integrated. We commit ourselves to lay and safeguard the foundations for all employees of the GRAMMER Group.
We firmly condemn any form of discrimination or harassment in the workplace based on criteria such as gender, ethnic background, disability, nationality, religion, age, or sexual preference and identity.
We expect our employees to contribute to building a corporate culture marked by objective and fair cooperation.
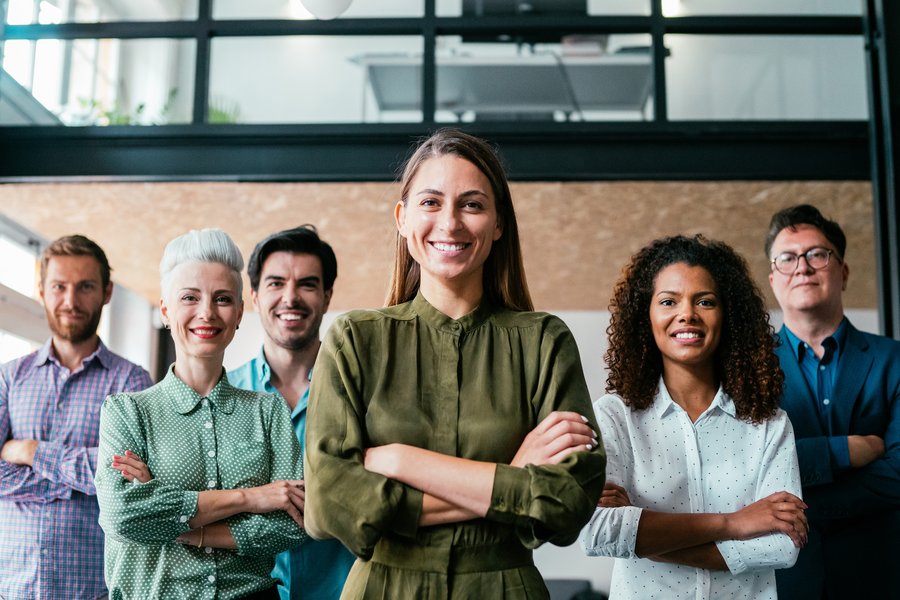
Charter of Diversity
We commit ourselves to cultivate an organizational culture, marked by mutual respect and appreciation for every individual. We are creating conditions under which superiors and employees alike will recognize, share and live these values. In this respect the executives resp. superiors have a special responsibility.
- To review internal HR processes at regular intervals and to ensure that these support the varying abilities and talents of all employees and our standards of performance accordingly.
- To accept the diversity of society within and outside our company, to value the potential inherent within these fields and using this in a way profitable to the company.
- To make the implementation of the Charter a topic of internal and external dialogue.
- To provide annual public reporting regarding our activities and progress in promoting diversity and respect.
- To inform our employees about diversity and to involve them in the implementation of the Charter.
Diversity Management – Strategic Objectives
Work-Life-Balance
By active support for the compatibility of family and work we encourage and give parents the opportunities to fulfill their professional goals.
Discover new opportunities
The intimate co-operation with universities, schools and educational institutions is intended to increase in particular girls’ and women’s enthusiasm for technical jobs.
Enlarge horizons
By promoting international operations and a transparent foreign assignment and re- integration policy we want to strengthen the networks between the skilled professionals and managers within our Group and thus increase mutual understanding.
Promote integration
By individual solutions all employees are given equal opportunities, to fully use their skills and abilities. For us, it is a matter of course to employ people with disabilities.
Think strategically
With the implementation of diversity management in the GRAMMER Group we want to ensure that we work together systematically in order to realize this commitment and that we develop permanently at all our locations.